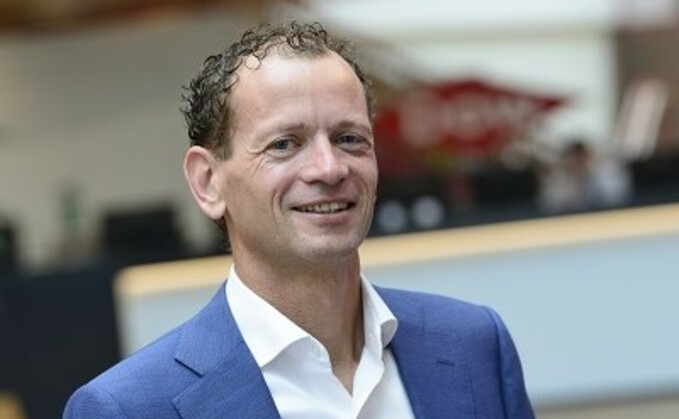
Industry Voice: Dow's Marco ten Bruggencate explains how the company is driving decarbonisation throughout its own business and the wider industry
From forest fires in Australia, to flooding in Germany, the effects of climate change are surfacing with ever greater frequency across the world. And with COP26 underway, now more than ever, we at Dow must decisively act to demonstrate our passion around environmental sustainability. Action is needed across all areas of society and business. We have an urgent responsibility and an imperative to ensure that everything we do as a company, is seen through the lens of sustainability.
We are accelerating our efforts to protect the climate, advance a circular economy and improve the safety and sustainability of our materials. But this isn't a decision we made overnight. We began our sustainability journey over 25 years ago, and since then have made good progress, particularly in cutting carbon emissions. But we must go much further, much faster. As the one of the leading producers of plastics, how we make our plastics has to be at the centre of our approach as well as ensuring that our products are recyclable, are getting recycled and contain recycled content.
Our commitments
By 2030, Dow will reduce its net annual carbon emissions by five million metric tons versus its 2020 baseline. And by 2050, Dow intends to be carbon neutral. If we can get there quicker, we will.
As part of our action plan to put us on a path to carbon neutrality, we are committed to implementing and advancing technologies to manufacture our products using fewer resources. Since 2005, we have reduced our overall greenhouse gas emissions by 15 per cent. And today, we are among the top purchasers of clean energy in the chemicals industry and in the top 20 globally. We're proud of that effort but again, we aim to do more.
Terneuzen - the Dow site leading the way to carbon neutrality
While Dow is working hard across every region to advance our sustainability commitments, our flagship site in Terneuzen, the Netherlands, is a fantastic example of the innovation paving the way forward.
We've developed a detailed roadmap for our Terneuzen site to reduce CO2 emissions from operations by more than 40 per cent by 2030, on our path to achieve net CO2 neutrality by 2050.
The first phase involves the construction of a clean hydrogen plant, where by-products from core production processes will be converted into hydrogen and CO2. The hydrogen can be used as an emission-free fuel in the production process, and the CO2 would be captured and stored, or re-used where possible until alternative technologies are developed. The hydrogen plant is expected to start up in 2026 and would allow Dow in Terneuzen to reduce CO2 emissions by approximately 1.4 million tonnes per year. The emissions saved would be the equivalent of taking more than 300,000 cars off the road each year.
The project will not only accelerate our journey to decarbonisation, but also bring important economic benefits, creating vital jobs in the green arena. Building the new hydrogen plant and the associated infrastructure is expected to create 3,500 to 4,000 engineering and construction jobs over a period of three years, and 400 to 500 permanent jobs at Dow and across associated service providers.
We also recently announced plans to build the world's first net zero carbon emissions integrated ethylene plant. The project would more than triple our ethylene and polyethylene capacity from our site in Alberta, Canada, while retrofitting the site's existing assets to net zero carbon emissions. It will enable us to decarbonise approximately 20 per cent of Dow's global ethylene capacity while growing polyethylene supply by about 15 per cent. It allows us to meet the increasing needs of customers and brand owners seeking to lower the carbon footprint of their products.
A game changing partnership with Shell
We're not stopping there though. In 2020, we embarked on one of our most exciting partnerships to date - a joint development agreement with Shell to develop electrified cracking technology that could be powered by clean energy. Cracking technology refers to the process by which longer hydrocarbon molecules are broken up into shorter, lighter molecules using heat and pressure and sometimes catalysts. Electrified cracking using renewable energy is a breakthrough technology that could dramatically reduce emissions across the industry - which is why the joint program has been awarded €3.5m in funding by the Netherlands government.
So why is this technology a game changer? Ethylene steam crackers supply chemicals used to make products that people use every day. However, today's steam crackers rely on fossil fuel combustion to heat their furnaces, making them CO2 intensive at present. Using renewable electricity to heat steam cracker furnaces could become an incredibly effective way to help decarbonize the chemicals industry. The challenge is to develop a technologically and economically feasible solution, and one which is scalable. Right now, we have global experts from Dow and Shell - and The Netherlands Organisation for Applied Scientific Research (TNO) and the Institute for Sustainable Process Technology (ISPT) through recently extended partnerships - working to design and scale 'e-cracker' technology, turning pilots into commercial crackers.
How else is Dow working to become carbon neutral?
Dow now manufactures products at 29 sites that are either fully or partially powered by renewable power purchase agreements. Recent agreements in Europe have added 10 sites to that list, transitioning all imported electricity to clean sources. The power supplied by the new agreements is expected to reduce Dow's Scope 2 emissions (which cover indirect emissions from the generation of purchased electricity, steam, heating and cooling) by more than 600,000 metric tons of CO2 per year.
We are embracing all forms of green power generation whether it's from small hydro, onshore and offshore wind, to large hydro, solar and biomass. Even just switching to imported renewable electricity at our site in Tarragona, Spain, is the equivalent of taking around 23,000 passenger cars off the road each year.
We're also looking at the feedstocks (the raw materials) needed to create plastics. Historically they are derived from fossil fuels - but that's changing. In addition to using circular feedstocks produced from waste plastics, using sustainably sourced and certified bio-feedstocks enables us to make plastic with significantly reduced CO2. We are working on several sustainable and certified sourcing options that allow us to produce bio-based plastics using other industries' residues or by-products.
So that's what we're doing on production - but what about the products themselves?
Protecting the environment while also reducing carbon emissions
It's fair to say that plastic packaging has a perception challenge. In part that's deserved, because as an industry, we have not been focussed enough on ensuring the circularity of our products. That's changing - and quickly. We are designing products so they are easier to recycle from the outset and investing heavily to scale innovative recycling technologies that can give plastics a second life rather than being lost to waste, incineration or landfill.
However, it's important to remember that plastic has been, and continues to be an incredibly useful tool in reducing carbon emissions. Particularly when it comes to combating food waste and driving distribution efficiency, which are significant global challenges. The UNEP Food Waste Index 2021 revealed that food waste alone generates 8-10 per cent of global greenhouse gas emissions. Our packaging innovations designed for food allow us to keep meat fresh up to three times longer, while using only a third of the packaging material compared to conventional methods. The result is a 75 per cent cut in both CO2 footprint and food waste compared to alternative packaging materials.
That's not to say that plastic is the answer to all packaging needs, and it should only be used when it offers the lowest environmental impact. But we need to recognise its positive performance on CO2 compared to other alternative materials and work to find the balance between CO2 emissions and circularity.
Aligning with EU policy on climate change plans and industry transformation
The European Commission's Green Deal sets a clear direction of travel: Europe will become carbon neutral by 2050 and accelerate the circular economy for all industries. The EMEA region which I lead for Dow is in the driving seat to turn the corner on this challenge. Our region will contribute significantly to our global goal of reducing CO2 emissions by five million tonnes by 2030 and will enable Dow's carbon neutrality goal by 2050.
A carbon neutral future that works for people and the planet
It is important we recognise the cost of inaction to address the climate crisis, not only on our planet, but also on the future of our industry and our company.
The complexity of the challenge is such that only through the collaboration of industry, academia, government and others, can we achieve the shared goals of the Green Deal. Only by working in partnership at each stage of the supply chain will we effectively address the challenges we collectively face. Partnerships between government and industry are increasingly important to incentivise investment in carbon reduction technologies - it is only through continued investment and innovation that we can create and scale decarbonising technologies.
We're on a journey of improving and innovating to tackle challenges such as this, with the spirit of Dow and our committed team of progressive thinkers and talented scientists leading the charge. I'm proud of the insight and action my colleagues contribute each day. I believe we're in a powerful position to affect real change, improve our environmental and climate performance and pave the way for the chemicals industry towards a more sustainable and carbon neutral future.
As we continue to produce materials important for everyday life, we will keep the planet and people at the forefront of all we do.
Marco ten Bruggencate is commercial vice president for packaging & specialty plastics EMEA at Dow.
For more details of our sustainability efforts and innovations in all sectors of Dow's activity across the world, head over to Dow.com.
And for more information about how Dow is revolutionising the way we recycle and progressing to a circular economy for plastics, read my previous articles for BusinessGreen. This article is sponsored by Dow.